Taste, passion and pride – these three attributes encapsulate the mission statement of the privately-owned De Brabandere Brouwerij from Belgium.
At the beginning of February 2017 De Brabandere commissioned a new bottling line from Krones; and this line is something “distinctively special” for Yves Benoit, the Brewmaster and Automation Manager at De Brabandere.
Great beers
De Brabandere is an expert when it comes to brewing a most varied range of different beers in many, sometimes out-of-the-ordinary flavours. The raw materials used are exclusively top-quality barley and wheat malts, and flavour-hops pellets (no extracts!) from Saaz, Hallertau and Tettnang – a consideration of paramount importance for the brewery and its three brewmasters Yves Benoit, Chris Van Acker and Pieter Maes.
It’s two things above all that make it into something rather special: firstly, with its hourly output of 35,000 bottles, it replaces two older low-speed Krones lines at a stroke. And secondly, the integrated Varioline is instrumental in successfully coping with the brewery’s high level of pack diversity – on just a single line, mind you. “In the future, thanks to this line, we shall again be in a position to fill more special private labels, the way we used to in our early days,” says Yves Benoit. It looks as if he could very well be right, because the new line has made many things a whole lot easier.
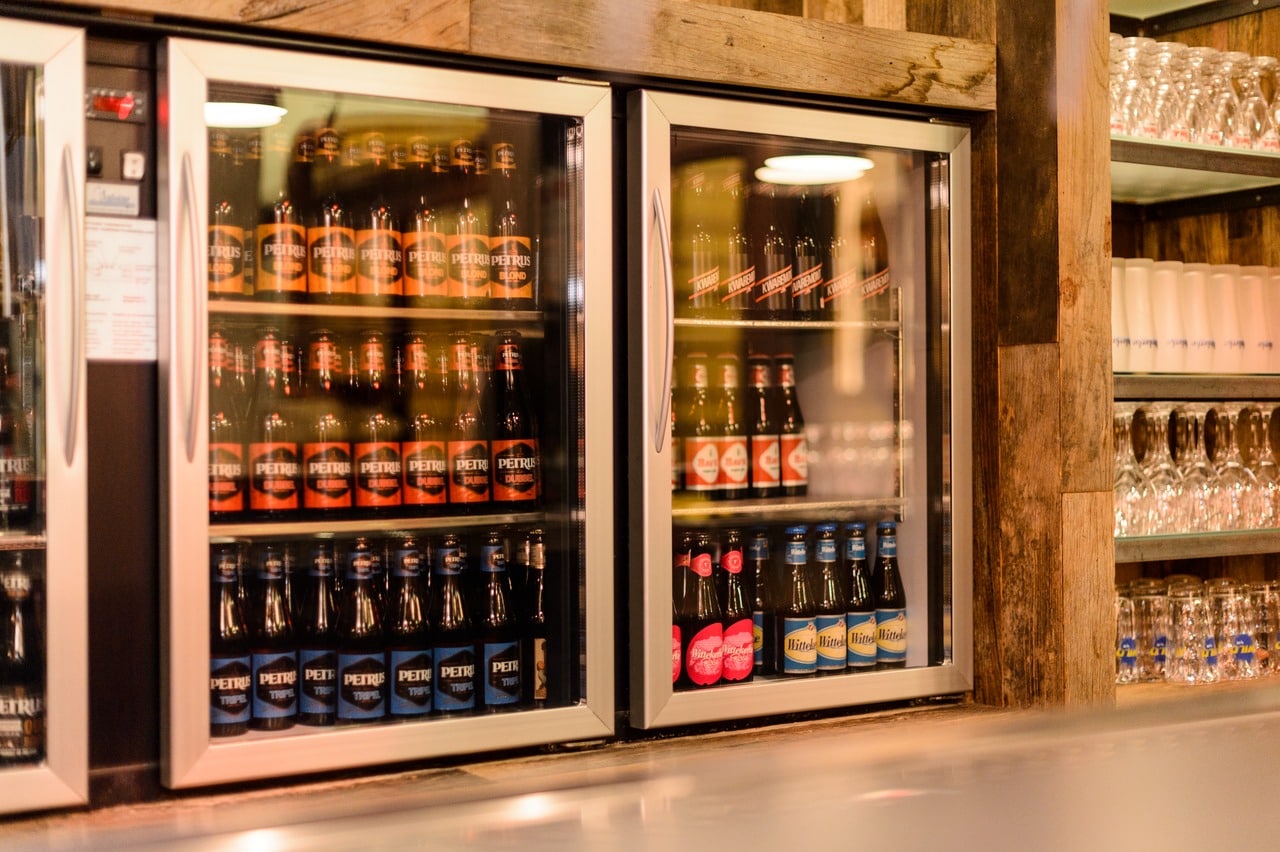
As the brewmaster explains: “The line enables us
- to fill the containers while they’re still warm. This means the bottles stay dry, can be more accurately labelled, and packed directly into cartons;
- to achieve a better bottling quality by reducing oxygen pick-up;
- to enhance fill-level accuracy;
- to automatically reject foreign bottles;
- to reduce staffing levels, and above all
- to upgrade flexibility, for end-of-the-line packaging in particular.”
A meticulously executed job
Planning, implementation and finally commissioning extended over a period of two years. The brewery’s wish to both produce packs with top-clips and then place these into crates and cartons, and to handle baskets and cartons as well, posed one rather special challenge. “We found that there were in fact several individual machines for this purpose, but none of these met our performance criteria,” says Yves Benoit, looking back. “This is why we changed our defined objective, and concentrated our efforts on finding a single machine that can do all the things we want.”
And that left only Krones. What I particularly appreciate with Krones is the meticulous way they work. With the line we’ve got today, we quite definitely have the best solution for our needs.
Yves Benoit
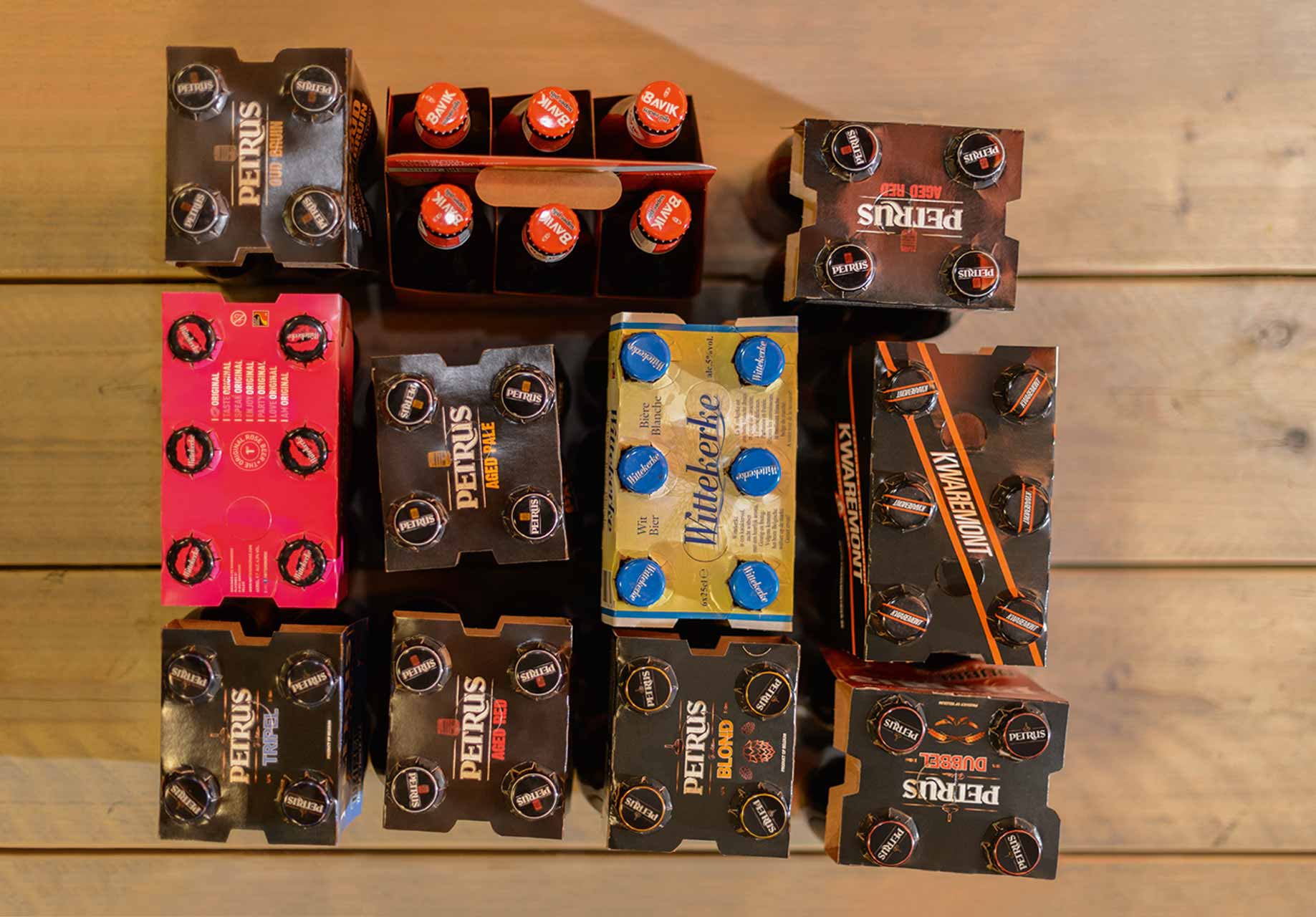
Maximised flexibility
It’s not just the packaging system, though, but the entire line that now gives De Brabandere a significantly higher degree of flexibility in its production operation: hitherto, the cold-filled bottles were packed exclusively in crates, because they were still too moist for cartons. The crates were then taken to repacking stations where employees repacked the bottles into cartons by hand – quite a laborious job.
Now Krones has installed a flash pasteuriser that prewarms the beer to 16 degrees Celsius. The downstream filler has been designed so as to ensure it can cope with the concomitantly higher filling pressure, of five to six bar. After filling, three concatenated Linadry machines make sure that the bottles are absolutely dry before they are labelled and then packed into cartons. In this way, the work sequences involved have been substantially simplified and speeded up, with the quality of packing being significantly enhanced into the bargain.
A definite favourite
And Yves Benoit is veritably entranced with the Varioline: “It’s the ultimate luxury for a brewery of our size.
- We can supply our customers faster.
- The quality of the packaging is better, and the automated packaging function is significantly more affordable.
- We cause a smaller CO2 footprint, since intermediate transports are no longer needed.
- The Varioline can be swiftly modified, i.e. in 15 to 20 minutes, to handle different formats.”
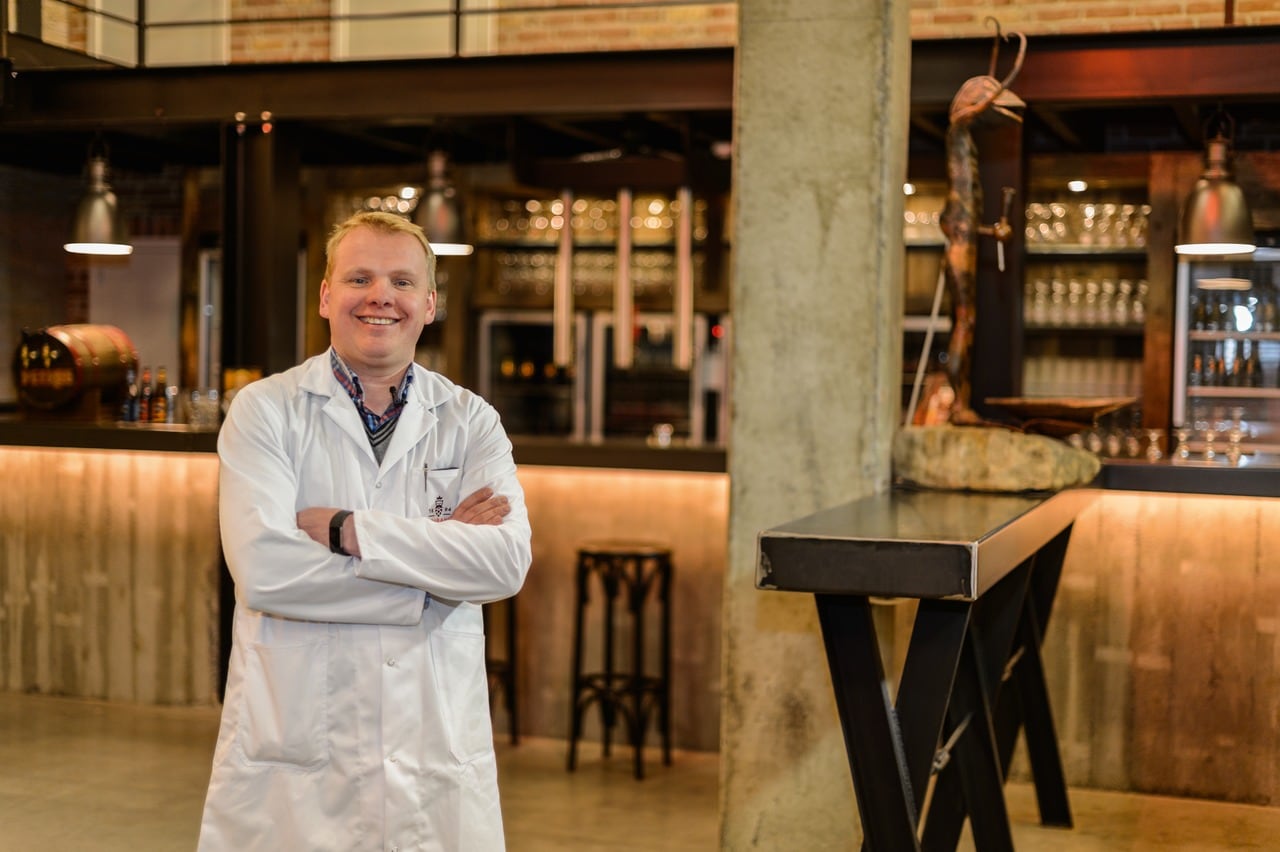
A complex line
The new line is accommodated in a refurbished warehouse on an area of 2,000 square metres. The highlights are:
- A machine installed upstream of the Linapac 2 unpacker that checks the proportion of foreign bottles in the crates
- Modulfill HES filler with 110 filling valves whose probes can be automatically adjusted to three different fill levels
- Varioline 3M
In addition, Krones also supplied the process-engineering kit, including
- a VarioFlash pasteuriser for warming or pasteurising the containers;
- two Contiflow units – one for carbonating beer, and one for water and soft drinks.
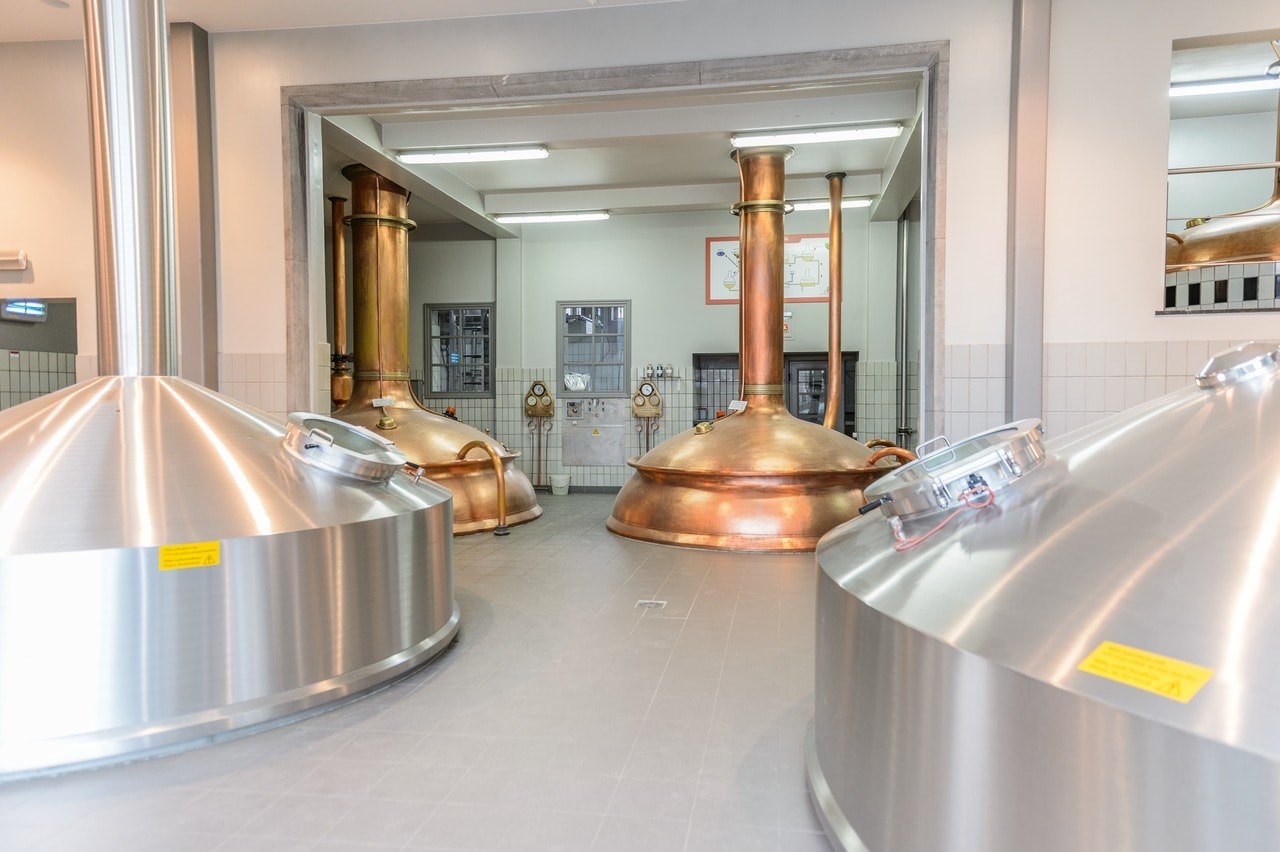
Wouldn't that be something for you too?